A Panoval Label S.A. foi fundada originalmente em 1991, na Suíça. Com base nos pontos fortes da empresa no Extremo Oriente, a Panoval (Ásia) foi estabelecida na cidade de Ho Chi Minh, no Vietname, em 2017. Esta instalação de última geração construída especificamente inclui várias linhas de revestimento e uma sala limpa com certificação ISO Classe 6 para produtos de alta qualidade que exigem o que há de mais moderno em tecnologia de revestimento. A empresa também é certificada pela ISO 14644-2.
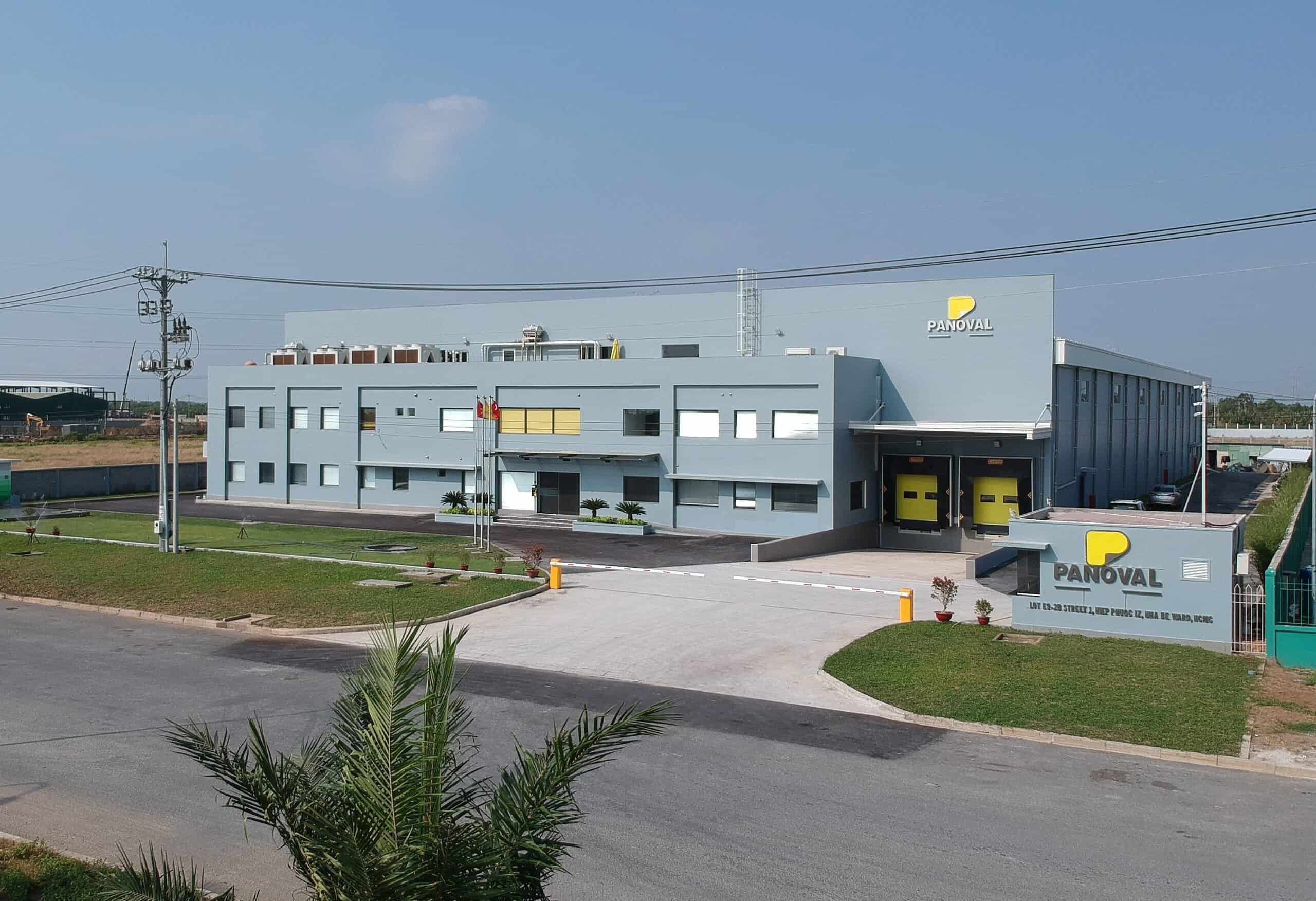
Mais de 60% do volume global de etiquetas adesivas sensíveis à pressão são produzidas no Extremo Oriente, incluindo aquelas para aplicações eletrónicas, médicas e farmacêuticas. Esta é a principal razão pela qual a empresa foi fundada no Vietname, embora a propriedade global continue a ser europeia. Apesar de ter apenas uma unidade de produção, a Panoval trabalha internacionalmente com revendedores e clientes diretos e construiu um negócio com presença global. Sua agilidade de produção e reputação de flexibilidade fizeram com que se tornassem um fornecedor líder de estoque de etiquetas especializadas e não padronizadas. Os clientes típicos são revendedores de embalagens flexíveis, conversores de etiquetas e impressoras convencionais.
Panoval emprega atualmente 25 pessoas e está em constante expansão. A equipe de gestão é composta por profissionais experientes e com atuação internacional, com ampla experiência no desenvolvimento e produção de laminados de etiquetas para as aplicações mais exigentes. O Diretor Wilco van Zwieten ingressou na Panoval como Gerente de Vendas em 1993 e agora é uma parte fundamental dessa equipe. Sua missão é impulsionar novos negócios e ele vê o avanço tecnológico e a inovação como fundamentais para seu sucesso. Como ele explica: “Num mercado tão competitivo, é o tamanho relativamente pequeno da empresa e a operação de duas linhas de revestimento muito diferentes que nos permitem ter tanto sucesso. Além do trabalho principal de maior volume que realizamos, nossa equipe de produção é capaz de executar uma infinidade de trabalhos especializados menores, às vezes trocando de produto três ou quatro vezes por turno. Usamos a mais recente tecnologia UV hot melt para respaldar nossos sistemas à base de borracha. Esta tecnologia UV é a única que pode potencialmente substituir os revestimentos à base de solventes… não imediatamente, mas dentro de dez a quinze anos. Para fazer isso, você precisa ter uma solução de cura UV de última geração com todos os recursos que respaldam essa tecnologia. E foi isso que projetamos, em colaboração com os fabricantes de máquinas e a GEW, para que possamos atender a todas as nossas necessidades nos próximos cinco a dez anos. Estamos preparados para o futuro.”
Projetado e fabricado no Reino Unido pela GEW, o sistema de cura UV personalizado da Panoval inclui cinco cabeçotes de lâmpada NUVA2, com capacidade para acomodar até sete cabeçotes no total, montados contra um rolo resfriado de Ø1000 mm em uma linha de revestimento Sung An Machinery (SAM). As lâmpadas são montadas ao redor do tambor em um conjunto de estrutura sólida, que é separado do conjunto de rolos e desliza para longe de sua posição engatada nos trilhos. Isto permite o acesso à superfície do rolo e à parte inferior do conjunto do cabeçote.
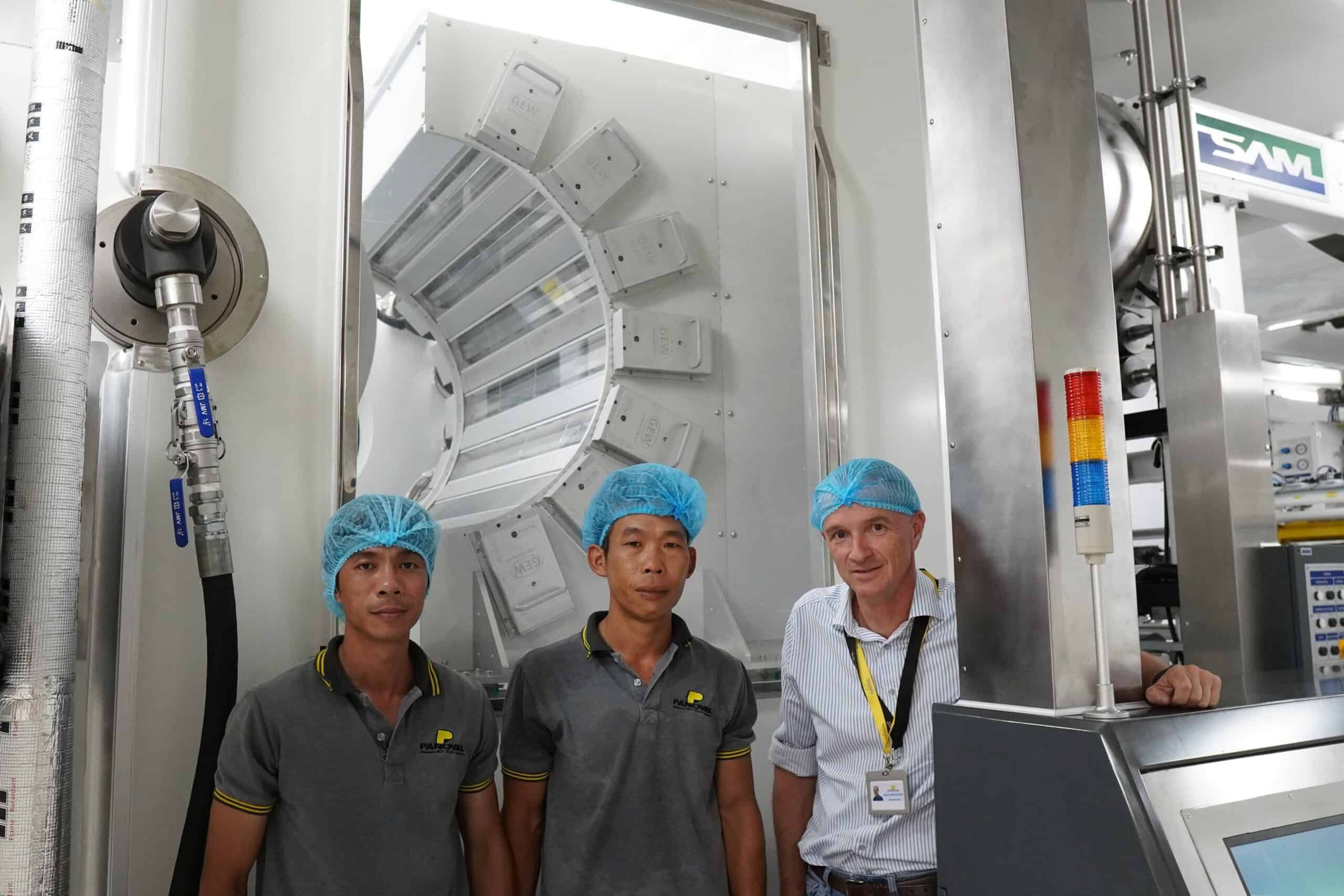
Ao procurar inicialmente uma solução de cura UV, van Zwieten foi direcionado à GEW por um associado da Malásia que havia trabalhado recentemente com a GEW para o projeto e instalação de um sistema de cura UV para aplicações de revestimento antiaderente. Van Zwieten relembra: “Visitei a fábrica na Malásia para ver a instalação em primeira mão e depois comecei a conversar com a GEW. Lentamente no início, pois sabíamos que precisávamos de uma solução complexa e projetada com um alto nível de personalização.” Gradualmente, o impulso foi aumentando à medida que ele trabalhava nos requisitos da Panoval com a divisão “Specialist UV” da GEW. Ele comenta: “Ficamos impressionados com o pessoal da GEW… sua capacidade de resposta e sua capacidade de responder a todas as nossas perguntas, por mais técnicas que sejam. É tudo uma questão de trabalhar com as pessoas certas.”
Van Zwieten visitou então as instalações de produção da GEW no Reino Unido durante a construção do sistema, o que proporcionou a ambas as partes a oportunidade de discutir o sistema em mais detalhes e garantir que ele estava no caminho certo para atender a todos os requisitos e expectativas. Em relação ao design, instalação e suporte técnico contínuo do sistema, van Zwieten não tem reservas: “Todo o processo foi perfeito, não tivemos nenhum problema. Se surgir um problema técnico, temos o monitoramento remoto do GEW para nos ajudar – mas realmente tivemos uma boa experiência com este sistema. E continua: “Até o momento, a única procura que temos tido pelo serviço de monitorização remota são os relatórios semanais que recebemos automaticamente, que nos mostram informações úteis de gestão, como tempo de funcionamento, horas de lâmpada, consumo de energia e eficiência. Também nos dá tranquilidade porque sabemos que se surgisse um problema, seria imediatamente sinalizado pela plataforma de monitorização.”
Como salienta van Zwieten, nenhuma despesa foi poupada na especificação do novo sistema de cura UV, para garantir que ele atenderá a todas as demandas nos próximos anos. Ele comenta: “Um laminador típico instala uma ou duas estações de lâmpadas e fica feliz. Diferimos aqui e instalamos uma série de cinco lâmpadas em conjunto, o que significa que podemos modificar a distância entre a aplicação química e a cura de um trabalho para o outro, permitindo-nos atender a muitos mercados diferentes que atualmente não podem ser atendidos com esta tecnologia. É por isso que escolhemos trabalhar em conjunto com o pessoal da GEW, pois eles possuem o conhecimento técnico e a experiência para um sistema tão complexo. Esperamos agora um rápido retorno do nosso investimento, com a poupança de energia e o novo trabalho que o sistema UV nos traz.”
Os mercados-alvo da Panoval são as indústrias farmacêutica e eletrônica, que exigem um rótulo mais limpo com menores propriedades de emissão de gases residuais. Van Zwieten explica: “A libertação de gases residuais ocorre quando um produto continua a emitir gases após a produção, e isto pode ser um problema sério para os fabricantes. No mundo da eletrónica, por exemplo, a libertação de gases pode causar falhas eletrónicas e se estiver a fabricar itens caros, como unidades ópticas, qualquer fator de falha terá de ser reduzido a um mínimo absoluto, caso não possa ser completamente erradicado.” Ele continua: “É aqui que o sistema de cura UV realmente nos diferencia. Tentamos e testamos nosso processo de cura em nosso ambiente de produção de sala limpa ISO 6 e podemos produzir laminados com propriedades de liberação de gases muito, muito mais baixas. Isso nos permite oferecer um produto mais limpo e muito superior a esses fabricantes especializados e seus conversores.”
Com o sistema UV personalizado projetado especificamente para Panoval, a distância entre as cabeças de revestimento e as lâmpadas de cura pode ser controlada com precisão. Isto significa que a exposição ideal pode ser alcançada para uma infinidade de aplicações diferentes. Além disso, o sistema UV foi concebido com sete alojamentos de cabeças de lâmpada e cinco cassetes de lâmpadas reposicionáveis, o que significa que as cabeças de lâmpada podem ser colocadas em diversas posições diferentes, para controlar eficazmente o tempo de permanência. Ao aumentar o tempo entre a aplicação de produtos químicos no substrato e o ponto em que esses produtos químicos são curados, isso permite mais tempo para que gases indesejados escapem antes da laminação. Também afeta a velocidade com que a máquina pode funcionar; o período de desgaseificação mais longo permite que uma cura eficaz e segura seja alcançada em velocidades de operação até 50% mais rápidas. Como diz van Zwieten: “Isto dá-nos uma enorme vantagem competitiva sobre muitas empresas norte-americanas e europeias, que estão limitadas a operar a velocidades mais lentas”.
Demonstrando a busca da empresa pela solução perfeita, a Panoval também investiu na instalação de cinco sensores GEW de monitoramento UV multiponto (mUVm) em cada um dos cabeçotes de lâmpada UV e vinculados ao seu sistema ERP. Eles podem medir na posição central da lâmpada e nas bordas extremas de uma alma de 500 mm e de uma alma de 1050 mm. Além das leituras do medidor de partículas que medem com precisão os níveis de liberação de gases imediatamente após a cura, o mUVm permite que a equipe de produção meça e verifique se o nível correto de dose e intensidade de UV foi administrado durante toda a produção. Com o mUVm é possível gerar um certificado de cura UV para cada lote, registrando as saídas UV ao vivo para cada lâmpada. Os dados de saída UV em tempo real são exportados por meio de uma interface API RESTful.
No entanto, o objectivo de van Zwieten é desenvolver ainda mais os benefícios do sistema de monitorização UV, utilizando a sua capacidade de relatórios para pesquisar e estabelecer níveis de energia ideais para aderência inicial, adesão e libertação da gama principal de produtos da empresa. As informações do sensor UV serão então usadas para criar um mapa de cura 3D de cada rolo enorme de produto, oferecendo um alto nível de rastreabilidade aos fabricantes usuários finais. Embora estes dados sejam particularmente cruciais para clientes das indústrias farmacêutica, eletrónica e aeroespacial, também podem ser utilizados para configurar execuções de produção repetidas, de forma rápida e eficiente.
A equipa de Wilco van Zwieten também teve de superar dificuldades técnicas criadas pelas condições locais na cidade de Ho Chi Minh. Os 18.000 m3/h de ar utilizados para resfriamento são aspirados para a sala limpa vindos de fora do edifício, a uma temperatura ambiente de cerca de 35°C. Eles instalaram filtragem de dois estágios e cerca de 25 metros de dutos de entrada adicionais para reduzir a temperatura do ar, a umidade e quaisquer partículas contaminantes internas, antes que cheguem aos cabeçotes da lâmpada.
A equipe de produção é movida coletivamente por uma mentalidade pioneira; seu foco é usar pesquisa e desenvolvimento para criar produtos que ofereçam ao usuário final uma vantagem comercial. Um exemplo disso é a produção de substrato para etiquetas de pneus, usando um processo refinado de hot melt UV. Como explica van Zwieten: “Não usaríamos hot melt convencional para etiquetas de pneus, pois é bastante instável, especialmente em gramaturas mais altas. Isto faz com que o conversor tenha que reduzir a velocidade de conversão, pois as lâminas de corte ficam rapidamente contaminadas com adesivo. Em vez disso, aperfeiçoámos o processo de fusão a quente UV, através do qual podemos sobrecurar ligeiramente, para criar um adesivo de baixa aderência com uma adesão final muito elevada. Isso significa que o conversor pode produzir suas etiquetas de forma muito mais rápida e limpa. É uma situação ganha-ganha para nós dois.”

São os benefícios comerciais a jusante que diferenciam os seus produtos UV dos convencionais e mais do que compensam o custo um pouco mais elevado das matérias-primas à base de UV. Além disso, van Zwieten aponta para uma tendência de mercado que também está a seu favor: “Cada vez mais fabricantes de revestimentos estão a produzir polímeros à base de UV e estamos a ver os preços a cair rapidamente… já caíram mais de 40% nos últimos três anos. É uma questão de tempo até que o UV assuma o controle.”
O sistema de cinco lâmpadas da Panoval permite que a equipe adapte o processo de cura para cada trabalho, para obter subcura e sobrecura à vontade. Como explica van Zwieten: “Para determinados trabalhos precisamos de uma cura insuficiente e podemos fazê-lo simplesmente utilizando uma lâmpada no final do caminho. A vantagem disso é que estende o caminho em até 130 cm, o que dá tempo para que a liberação de gases ocorra antes que o revestimento atinja a estação UV. Assim, podemos produzir rótulos para aplicações médicas altamente exigentes, por exemplo, sem desacelerar a nossa linha de revestimento.”
Para quantificar este aumento de velocidade em termos de vantagem competitiva, van Zwieten continua: “Podemos executar estes trabalhos específicos a até 40 metros por minuto, o que está muito acima da norma para este tipo de produto especializado. Eles normalmente funcionam na Europa e nos EUA a 25 metros por minuto e, como resultado, são significativamente mais caros em produtos similares.”

A rotulagem para aplicações médicas é frequentemente necessária em substratos não tecidos, que absorvem muito mais radiação do que poliésteres e polipropilenos. Isso significa que o alto poder de cura UV também é um requisito regular, e a sobrecura é facilmente alcançada com até 108kW de potência UV disponível. A sobrecura UV é usada para imitar as propriedades mais desejáveis dos adesivos à base de solvente, em que o revestimento é curado para se tornar de baixa aderência e seco ao toque, mas ao mesmo tempo permanece um adesivo altamente coeso que envelhece extremamente bem. Este processo tem outras vantagens, como explica van Zwieten: “A aderência inicial é baixa e permite até mesmo o reposicionamento, mas a adesão final é muito forte – facilmente superior a 50 newtons – como é necessário para uma rotulagem de alto desempenho. E então voltamos às vantagens da conversão, que se torna um processo muito mais rápido com revestimentos curados por UV.” Ele conclui: “Podemos alcançar todos os benefícios dos revestimentos à base de solvente, mas sem a liberação de gases e os extraíveis, que são tão preocupantes para as indústrias médica, aeroespacial e eletrônica”.
A Panoval também possui janelas de quartzo GEW ‘HiC’ instaladas nos cabeçotes de lâmpada UV, que são particularmente adequadas para aplicações de hot melt. Este tipo especial de quartzo permite que uma quantidade significativamente maior de energia UVC passe para o revestimento, em comparação com o quartzo convencional. Como comenta van Zwieten: “Não cortamos nenhum atalho nas especificações do nosso sistema UV e ainda não encontramos um trabalho que ele não possa fazer. Como executamos uma gama ampla e diversificada de trabalhos exigentes e de curta duração, tínhamos de ter a certeza de que seríamos sempre capazes de alcançar o que pretendíamos. E se algum dia descobrirmos que precisamos de mais energia, poderemos facilmente adicionar mais dois cassetes de cabeçotes nos alojamentos vagos.” Ele acrescenta: “No entanto, do jeito que está, podemos correr a 220 metros por minuto nesta linha. Estamos alcançando o dobro da velocidade de produção de uma aplicação equivalente à base de solvente. Como exemplo, produzimos recentemente uma etiqueta removível de poliéster com um revestimento de baixa liberação de silicone a 100 metros por minuto com uma cobertura de baixo peso e zero emissão de gases… e isso, até onde sei, é um novo recorde mundial.”
“O sistema GEW alcançou exatamente o que queríamos. Ele cura demais, cura perfeitamente. Estamos a poupar enormes quantias em termos de consumo de eletricidade e a reduzir a nossa pegada de carbono. Se você imaginar que nosso antigo sistema à base de água exigia quase 40 metros de fornos aquecidos a 200 graus, para retirar a água… estávamos consumindo cerca de 1.800 kW por hora. Com revestimentos à base de água, cerca de 40% de cada quilo é água que precisa ser extraída. Agora com o UV podemos rodar a 220 metros por minuto e o máximo que consumimos gira em torno de 600kW por hora. Então é um terço.”
No entanto, há outras considerações a serem levadas em conta ao adotar processos de cura UV, como aponta van Zwieten: “Você precisa de pessoal mais bem treinado e dedicado para trabalhar e compreender os UV, e você precisa de equipamentos melhores para começar. Para efeito de comparação, existem mais de 1.100 laminadores à base de solvente somente na China e são máquinas básicas, de baixo custo e simples de operar. Você não precisa de um laboratório. Mas é um jogo perigoso – é tóxico e poluente e custa muita energia.” Comparando isto com os benefícios dos UV, ele conclui: “Com os UV não é necessário um incinerador, não é tóxico, não há risco de incêndio e as poupanças de energia e os benefícios ambientais são muito impressionantes”. Ele conclui: “Encontramos um parceiro muito competente e ágil na GEW. Para quem procura uma solução UV para adesivo hot melt, sugiro que ligue.”
Clique aqui para obter mais informações sobre nosso processo UV especializado.